KESCON Engineering
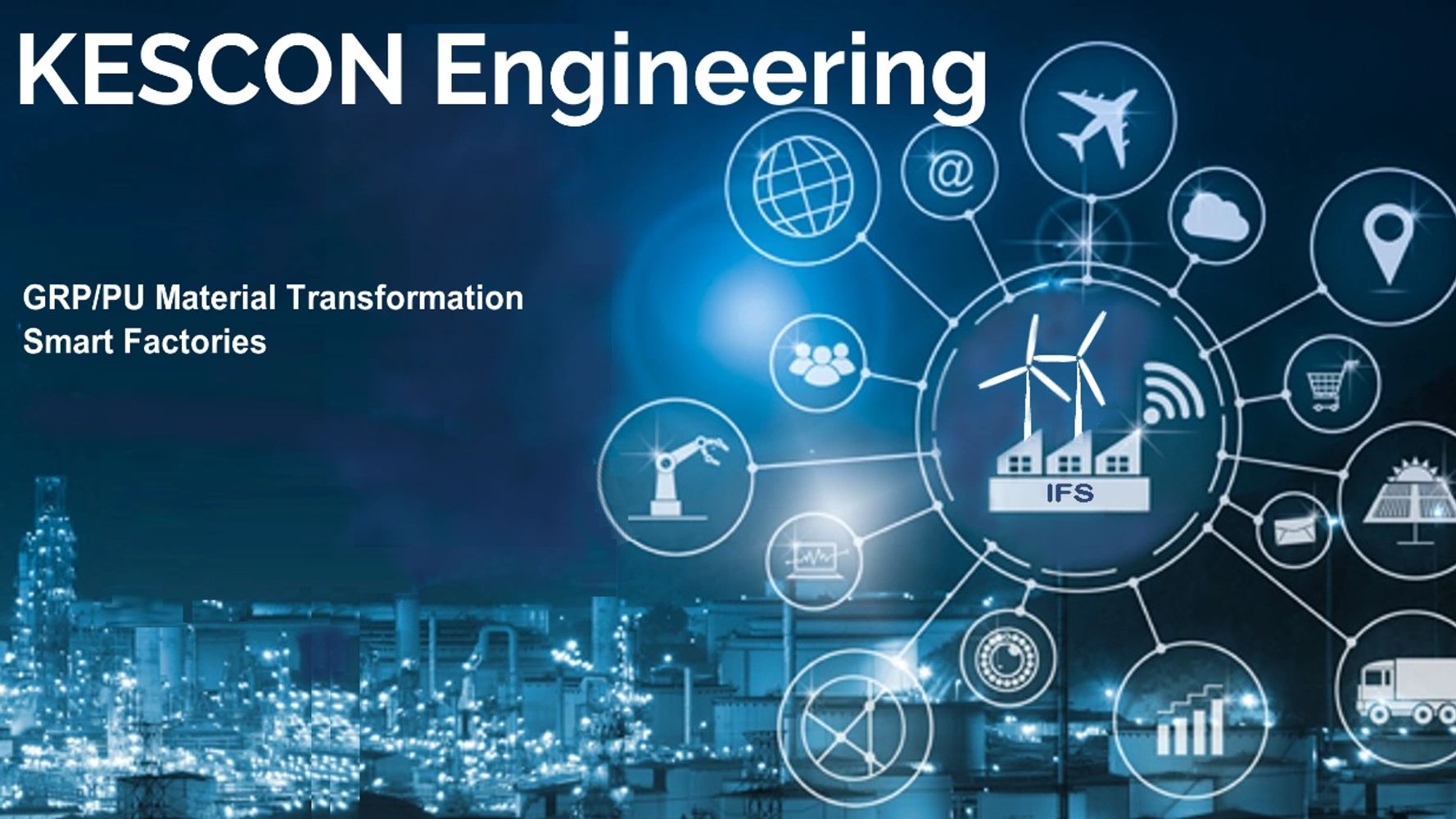
KESCON Engineering is focused on the design and layouts for the true Material Transformation projects, while still serving traditional composite panel projects internationally.
UPCYCLING is what's needed today. KESCON Engineering is focused on building Smart Factories today with decades of experience in Material Transformation.
We have deep knowledge and experience working with different composite materials.
Wind Blades primarily made out of fiberglass. At the EoL Wind Blades present a major issue for the industry. At IFS we know, fiberglass composite materials CAN be recycled.
These are not sustainable solutions and can't be categorized as the final answers. CO2 free energy and burning of waste don’t fit together.
Upcycling is the Material Transformation, which is a much more sustainable solution.
This technology assures significant CO2 savings in contrast to virgin GRP production and current Co-processing (incineration) methods.
This is just one example of the many high-end products that can be produced as part of the IFS material transformation process.
Recycled Polyurethanes Fiberboard (RPF) is a 3-layer composite panel, manufactured from recycled polyurethanes (mainly PUR, fiberglass, polyesters) and other components. The independent test results exceed all of the North American Laminated Flooring Association (NALFA) performance requirements for commercial flooring. The unique RPF properties include high moisture resistance, low thickness swell, excellent dimensional stability, and a closed, hard surface suitable for direct lamination. The RPF product is designed to be used for the commercial sector of the laminate flooring industry, but as a backup, has also been found attractive as a substitute for marine and CDX/MDO plywood, for end-uses in boats, tractor trailer doors and school bus flooring as well as for the production of sports flooring systems.
Since the RPF product is produced from 100% recycled Polyurethane waste materials including industrial waste from automobile manufacturers, and the end-of-life product may also be returned and recycled, it is certain that RPF qualifies for United States Green Building Council and Green Guard, Inc. certifications.
Reinhard Kessing, CEO & Founder
Studied Electrical Engineering, in Cologne, Germany.
First 15 years of my business life, I worked for BISON-Werke, Springe, Germany, a company that designed, built, & installed wood-based panel plants around the Globe. I quickly climbed the career ladder from double-E “Sparky” to Project Manager and finally to a Technical Director of BISON North America. Often times, I was confronted with many technical- and technological challenges, which I found great pleasure in solving. I was always pushing for innovations, which resulted in two (2) Patents issued for my work, but those were assigned to BISON.
Back in 1989, UNIFIX, Bromont, QUE, Canada (backed by "Bombardier” at the time) wanted to recycle a waste-polystyrene (styrofoam) by mixing it with cement, adding fiberglass mats, and creating a new, high-tech panel-board, suitable for construction applications. I took on this project. Overcoming many initial challenges, the project was a success. We have designed the production line as a continuous process. Today, the operation is a subsidiary of “National Gypson Comp.” UNIFIX is still producing today, 31 years later.
In 1992 I separated from BISON to focus on future-oriented business strategies and technologies. Partnering with two gentlemen, we found TURAIN Automation & Systems Inc. in Erie, PA, USA.
At TURAIN we provided innovative solutions for panel-board , plastics and composite industries. We gain deep knowledge, establish a wide networking system and saw many recycling opportunities.
Need for recycling was clear for a long time. Felling trees and wasting other valuable resources wasn't the answer for the future. In 1997, KESCON Engineering was selected and financed by the World Bank (IFC), to design and build the first true 100% wood-recycling project (BMK) in Takoradi, Ghana, West-Africa. The plant used 100% residues (approx. 150 tons per day) from nearby sawmills, veneer plants and lumber mills. BMK produced in a very efficient- and environmentally-friendly way, modern-style RTA furniture, kitchens, wardrobes and much more, all from 100% waste-wood.
In 2002 KESCON Engineering provided 100% of the plant-design, construction-supervision, start-up- and commissioning services for GreenTech Panels LLC. The first and only plant in North America to produce high-grade panels from 100% wood waste (EoL pallets, crates, construction waste, furniture, railroad ties, dunnage and much more).
More than thirty-five (35) years of international, hands-on experience with Composite Board manufacturing, machinery and customers around the world. Mechanical,- electrical and technological background allows offering of the full range of plant services: project-design, project-evaluation, project installations, project start-ups and commissioning, project retrofits and improvements and project appraisals. Hands-on experience with all forming- and press systems: Specialized in Continuous-, Multi-, and Single-Opening systems, as found in MDF, HDF, OSB, PB manufacturing.
Patents:
Ø 1990: Patent DE3826706A1 “Schleifverfahren für plattenförmige Werkstücke” (computer controlled sanding method for panel-boards)
Ø 1991: US Patent # 4,998,869 for “Apparatus for making particle mats with uniform weight distribution”
Ø 2009 Patent: US 7,527,865B2 “THREE LAYER COMPOSITE PANEL FROM RECYCLED POLYURETHANES”. (PRODUCT PATENT)
Ø 2010 US Patent: US 7,754,120 B2 (PROCESS PATENT) for the (above) three-layer RPF panel.
Besides traditional composite panel projects, KESCON Engineering designed and provided comprehensive engineering services for the following innovative recycling projects:
Ø GreenTech Panels LLC. 2002. Design, build, start-up of first and only plant in North America to produce a panel from 100% waste wood
Ø SaveWood LLC. 2005. The total departure from wood-based panels, developing material transformation technologies in the field of automotive- industrial polyurethanes and many other composites, which resulted in the production of a water resistant multi-layer panel, suitable as a substrate for laminate flooring and many other industrial applications.
Ø Global Fiberglass Solutions Inc. 2018. Design, layout, equipment selection and project engineering for the first plant in North America to produce panel-boards and pellets made from EOL wind-turbine blades
The Challenge can be overwhelming for just one party, that's why we believe in joint effort and cooperation between many industry sectors.
We all must do our part in keeping it alive and healthy.
Committed to your needs, ready for the challenge. We continue where others stopped.
WORLDWIDE SERVICES
info@kescon.de RHK@kescon.de kesconUS@aol.com DE: (+49) 170 532 3338 US: (+1) 325 236 2370
KESCON Engineering
Powered by GoDaddy Website-Baukasten